The manufacturing industry continues to transform each year. Shifting consumer demands, technology breakthroughs, and environmental expectations influence the entire manufacturing landscape. Many experts, including those at the National Association of Manufacturers, believe these changes will shape the future of manufacturing far beyond 2025.
According to Deloitte’s 2025 Manufacturing Industry Outlook, 62% of surveyed executives expect revenues to rise in the next 12 months, and more than half cite supply chain disruptions as a main concern. These figures highlight the ongoing need for adaptability and innovation.
We are in a manufacturing renaissance, with a once-in-a-generation opportunity to bring more production home, invest in our workforce, and strengthen our supply chains.
said Jay Timmons, President and CEO of the National Association of Manufacturers.
His words echo the sentiment that modern factories must adopt advanced technologies and resilient strategies to remain competitive.
This article walks through the top manufacturing trends 2025 and beyond, showing how manufacturers can get ready for the demands of tomorrow.
1. The rise of smart manufacturing and Industry 4.0
Smart factories have become a top priority for companies aiming to boost productivity and reduce waste. The current state of the smart manufacturing market shows prospects for years to come of this manufacturing industry trend (see Fig. 1).
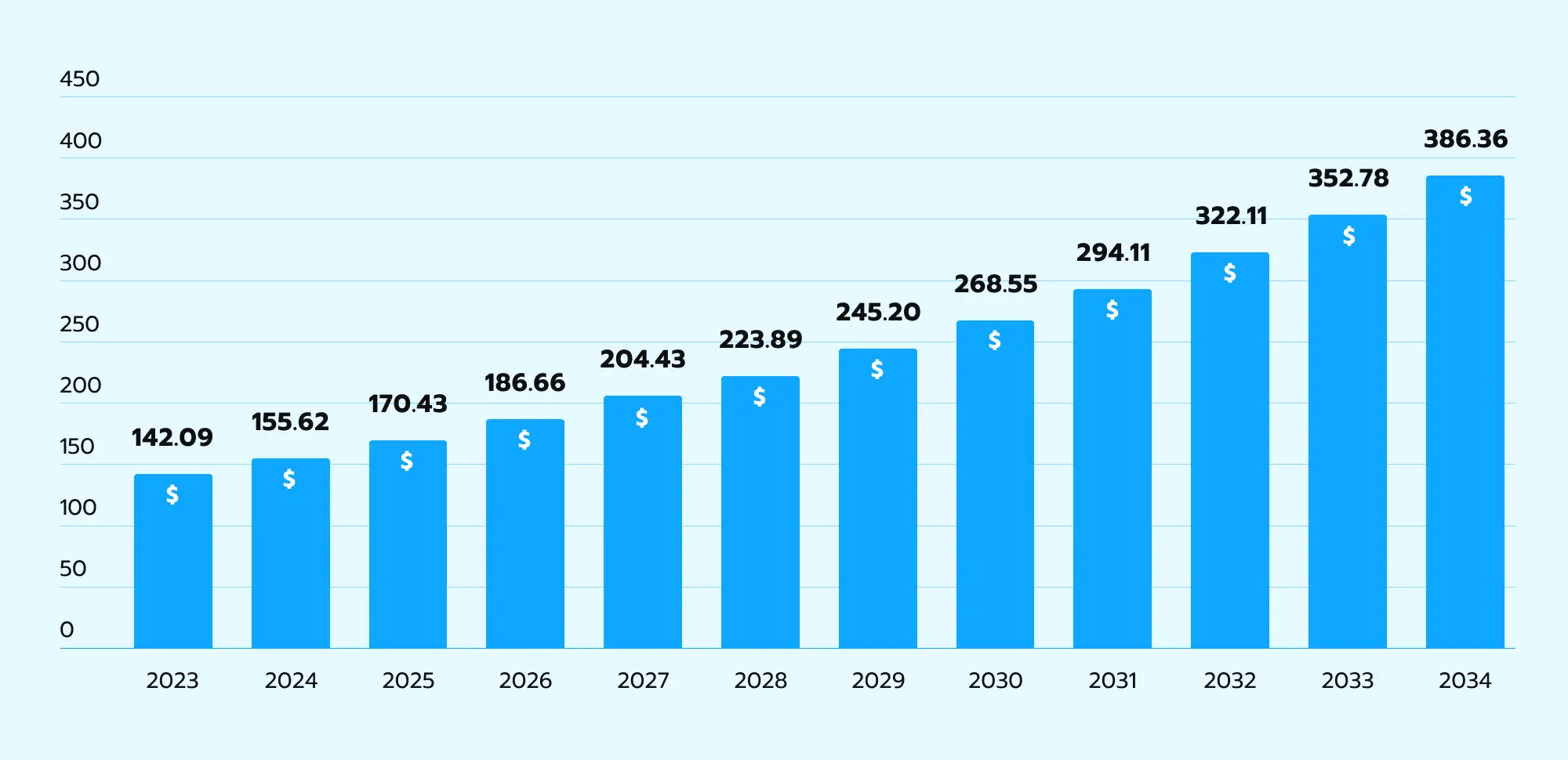
Figure 1. Smart factory market size in USD billion
These modern facilities rely on smart technology, connectivity, and data analytics to oversee every aspect of manufacturing processes. Smart manufacturing merges multiple innovations, including the Industrial Internet of Things (IIoT) and artificial intelligence (AI), to drive efficiency and better decision-making.
Data as a Resource
For manufacturers, data quality remains a significant hurdle. However, data is a crucial asset in modern operations. Sensors on production lines feed real-time information to cloud computing or on-premise systems, helping detect slowdowns, quality issues, and safety gaps. Many facilities now use machine learning models to analyze vast amounts of sensor data in seconds, allowing technicians to address issues before they escalate.
Industry 4.0 and Automation
Industry 4.0 goes beyond simple robotics; it focuses on connectivity between equipment, supply chain management platforms, and human operators. Automation plays a pivotal role, not only on the factory floor but also in back-office functions like inventory management and scheduling. Companies that embrace Industry 4.0 often see improvements in time-to-market, workforce satisfaction, and cost control.
Reskilling the Workforce
Digital transformation requires new skills. Manufacturers will invest in training programs to help employees gain the expertise needed for advanced manufacturing systems. As smart factories grow more sophisticated, shifting worker duties from repetitive tasks to oversight of automation becomes essential. This strategy reduces errors while maintaining human insight in key decision-making areas.
Smart manufacturing and Industry 4.0 rely on sensors, real-time data, and automation to build a more responsive, efficient factory. This approach upgrades the manufacturing line, boosts productivity, and supports a flexible workforce.
2. AI and ML. Revolutionizing Manufacturing Processes
AI is revolutionizing manufacturing, and it is as simple as that. Companies of all sizes see how AI can cut costs. Besides, everyone out there is trying to predict recent trends in manufacturing technology.
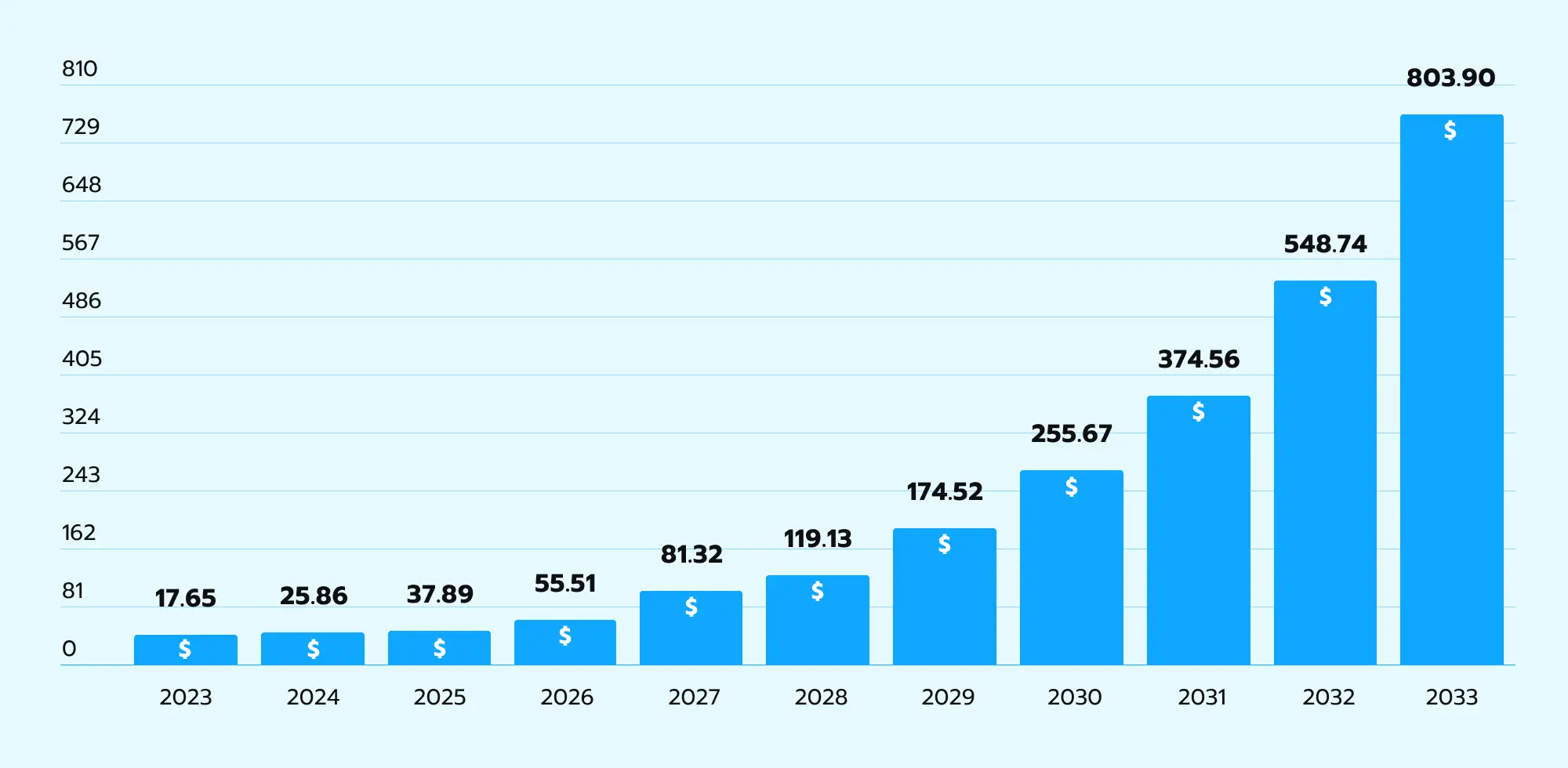
Figure 2. Gen AI market size in USD billions
According to this scientific article, AI is among the top manufacturing trends driving the industry’s move to adopt data-driven methods.
Predictive maintenance for reduced downtime
Traditional maintenance schedules can lead to costly inefficiencies. AI-driven predictive maintenance, powered by machine learning algorithms, monitors equipment health through sensor data. This allows factories to address issues before they lead to system shutdowns. The result is extended machine life, reduced repair costs, and continuous production flow.
Quality control and inspection
AI-powered tools improve inspection accuracy and speed. Systems similar to Magic Eye, which rely on computer vision, spot even minor flaws in products. These solutions help reduce waste by catching defects early. They also eliminate data quality issues that might arise if inspections depended solely on human input. Some automotive industry manufacturers use these AI-driven checks to maintain consistent standards while managing rising production volumes.
Supply chain optimization
AI supports inventory management and enhances supply chain resilience by enabling real-time analysis of orders, supplier lead times, and logistics routes. This analysis helps flag potential disruptions, allowing for quick adjustments in scheduling or sourcing to keep operations on track. Some global supply networks use advanced machine learning to balance demand fluctuations, regional regulations, and shipping constraints.
AI and machine learning also provide actionable insights, reduce waste, and enable predictive maintenance solutions. These capabilities help the manufacturing sector remain competitive and agile.
3. Digital Twins or improving efficiency before production begins
A digital twin is a virtual replica of a physical asset, process, or system. It lets manufacturers test changes, forecast outcomes, and adjust configurations in a risk-free environment. This idea and manufacturing trend have changed how companies approach planning.
The digital twin market is on the rise, and there are many prospects for the sector in the future (see Fig. 3).
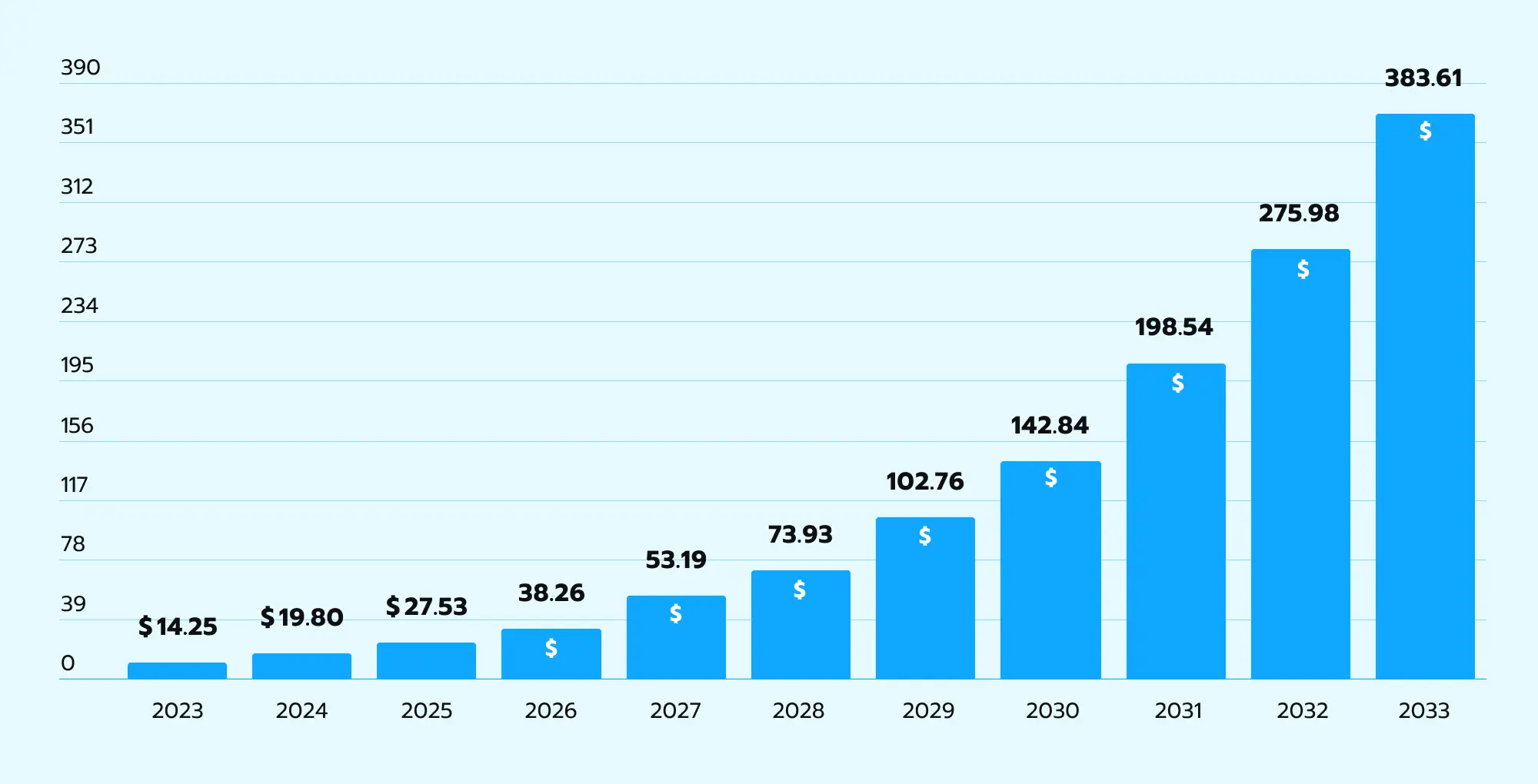
Figure 3. Digital twin market size 2023 to 2033 in USD billion
The phenomenon has offered some hefty perks in the context of the major market rise. Let’s examine these in greater detail.
1. Proactive problem-solving
Digital twins help manufacturers uncover bottlenecks in design and production before actual deployment. By modeling entire manufacturing processes, engineers can rearrange workflows, measure resource consumption, or assess how different materials might alter a final product.
2. Better collaboration
Digital twins enable teams from different locations to collaborate on the same model, enhancing global manufacturing coordination. This feature improves teamwork, reduces travel, and accelerates feedback loops. Cloud computing solutions allow for real-time data sharing, further helping teams refine strategies and designs.
3. Reduced development costs
By using digital twins, manufacturers can identify design flaws or inefficiencies early in the process. This proactive approach prevents costly changes later on. Additionally, digital twins help reduce waste by clarifying how each process functions, allowing factories to plan resource usage more effectively.
4. 3D Printing (additive manufacturing) and customization
3D printing, also known as additive manufacturing, is a trend in manufacturing, reshaping the way parts and products are made. Once limited to prototypes, it now produces final goods in the automotive industry, aerospace, medical devices, and beyond.
It is safe to say that 3D printing in manufacturing is the next big thing. Just consider the skyrocketing market size in North America alone (see Fig. 4).
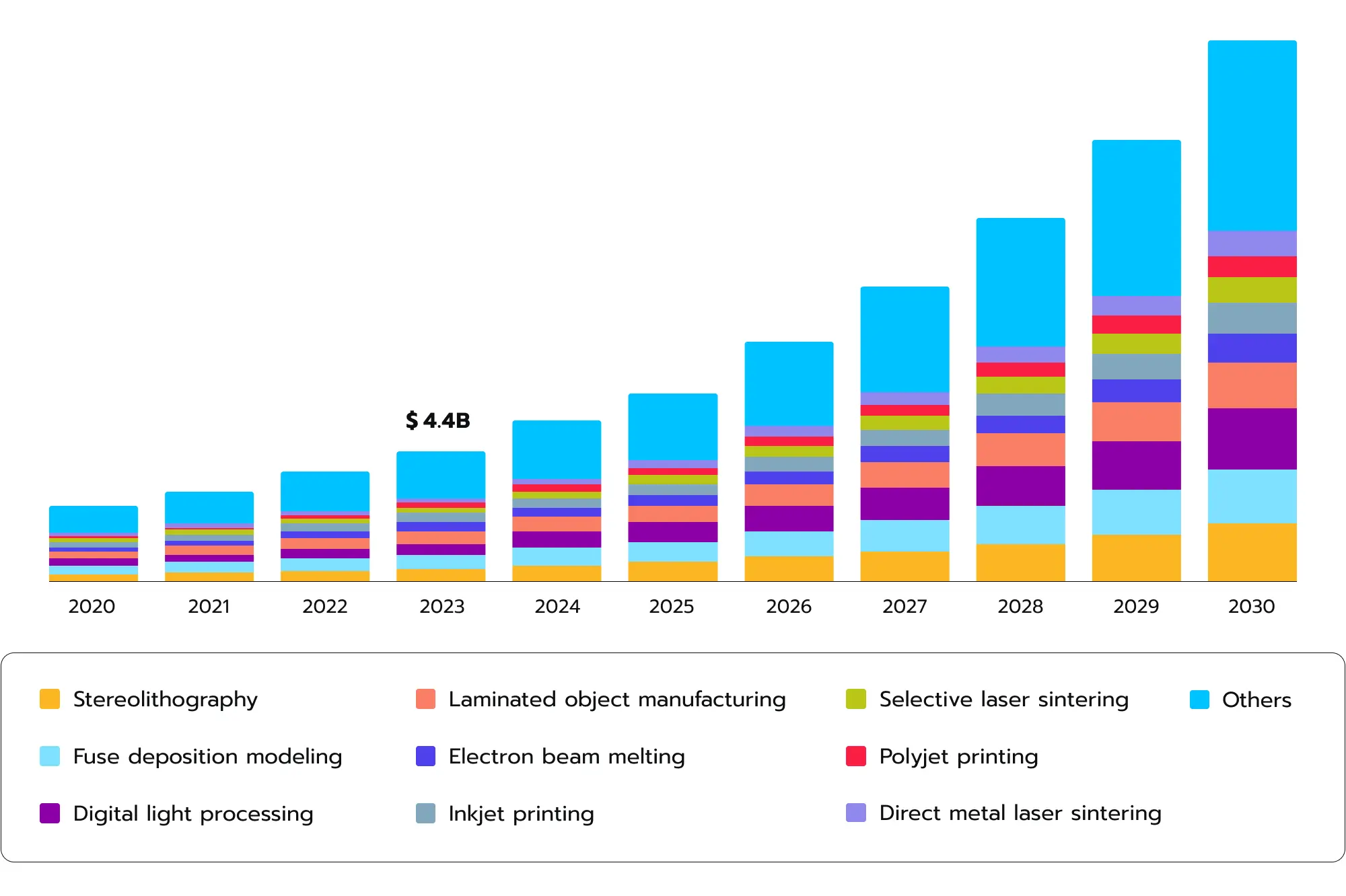
Figure 4. North American 3D printing market size in USD billion
Considering the fast-improving market, 3D printing has proved to be the sector offering some distinct advantages:
Rapid prototyping and production
3D printing allows fast production of prototypes. This speed helps companies refine product designs without waiting weeks for tooling or molds. It also cuts costs related to retooling entire manufacturing equipment for small production runs.
Customization at Scale
Consumers increasingly demand personalized products, and 3D printing makes on-demand customization possible. This is especially beneficial for businesses producing specialized components, such as medical implants or parts for limited-edition vehicles. By setting up additive manufacturing cells in key markets, manufacturers can shorten shipping times and respond quickly to changes in demand.
Reducing material waste
Traditional manufacturing sometimes creates leftover material that ends up as scrap. Additive manufacturing deposits only the material needed to form a part. This feature aligns with green manufacturing goals by using fewer raw materials and reducing waste.
3D printing supports lean manufacturing by reducing materials, speeding up design iteration, and enabling customization. It’s a strong option for companies that want flexibility and efficiency.
5. Green manufacturing and sustainability goals
Many manufacturers strive for carbon neutrality as they navigate changing consumer expectations and environmental regulations. There are existing guidelines serving all companies out there. These can help establish green manufacturing as a solid manufacturing trend.
In this case, green manufacturing aims to reduce waste, cut emissions, and rely on renewable energy sources. To understand whether sustainable manufacturing works, we need to understand the growing demand for the approach. The evidence shows at least an 11% compound annual growth rate (CAGR) within the market (see Fig. 5).
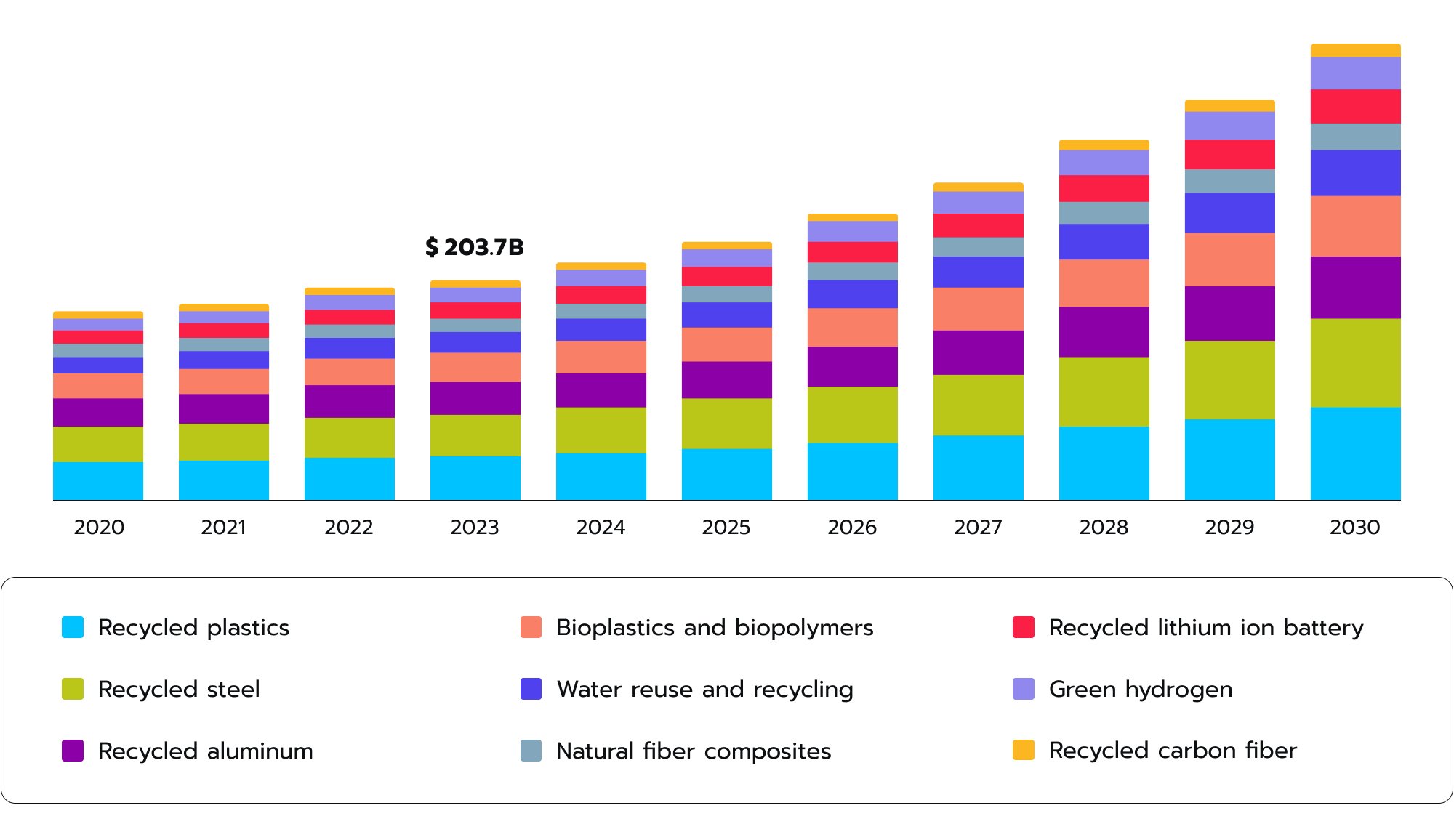
Figure 5. Sustainable manufacturing market size in USD billion
The push toward more sustainable operations helps manufacturers stay compliant and resonate with eco-conscious buyers.
Renewable energy integration
Solar panels, wind turbines, and other renewable energy sources power factories seeking to shrink their carbon footprint. Companies often combine on-site renewable generation with energy storage systems. Excess energy can be returned to the grid, lowering overall costs.
Sustainable materials and processes
Some manufacturers are shifting from traditional materials to eco-friendly alternatives. Recycled metals, biodegradable plastics, or organic coatings all help reduce waste. These changes enhance sustainability without sacrificing product performance.
Circular economy approach
TThe circular economy focuses on reusing and recycling materials to extend product lifecycles. By keeping resources in use for as long as possible, this approach reduces the consumption of virgin materials and lowers energy use in manufacturing facilities. This strategy aligns with global manufacturing trends, helping preserve resources and address environmental concerns.
Green manufacturing and sustainable practices are no longer just niche concepts; they have become essential for any manufacturer aiming to shape the industry’s future while maintaining compliance and cost-effectiveness.
6. Supply chain resilience and reshoring efforts
Supply chain disruptions have prompted a closer look at manufacturing footprints. Recent events, including the pandemic, revealed how vulnerable global supply chains can be. Manufacturers are weighing reshoring or bringing production closer to home as they balance cost and flexibility.
Such a manufacturing industry trend can potentially bring some tangible benefits:
Regional production
Reshoring reduces reliance on distant suppliers. Companies cut shipping times and face fewer uncertainties tied to trade policy shifts. This approach can help with inventory management by allowing plants to respond quickly to local demand fluctuations.
Supply chain optimization
Many experts define supply chain resilience as the ability to handle disruptions without shutting down production lines. This might involve diversifying suppliers, storing strategic inventory, or using advanced analytics for real-time shipment tracking. McKinsey predicts that a more localized approach protects against extreme global events.
Supporting local economies
Regional production can raise wages and create jobs, fostering goodwill among consumers who want local options. It can also shorten lead times, reduce shipping costs, and strengthen the manufacturing workforce by providing stable employment and room for reskilling.
Supply chain disruptions will continue to be a concern. Many firms are turning to reshoring and localized production strategies to reduce dependence on long-distance suppliers and boost agility.
7. Robotics and automated manufacturing equipment
Robotic arms and automated systems are now on countless factory floors. They handle repetitive tasks, reduce physical strain on human workers, and reduce error rates. Researchers at Deloitte note that industrial robots have spread from automotive production lines to the consumer electronics, food, and textile sectors.
The doubling of robot density in the manufacturing industry is the best indication that robotics have a bright future in the industry (see Fig. 6).
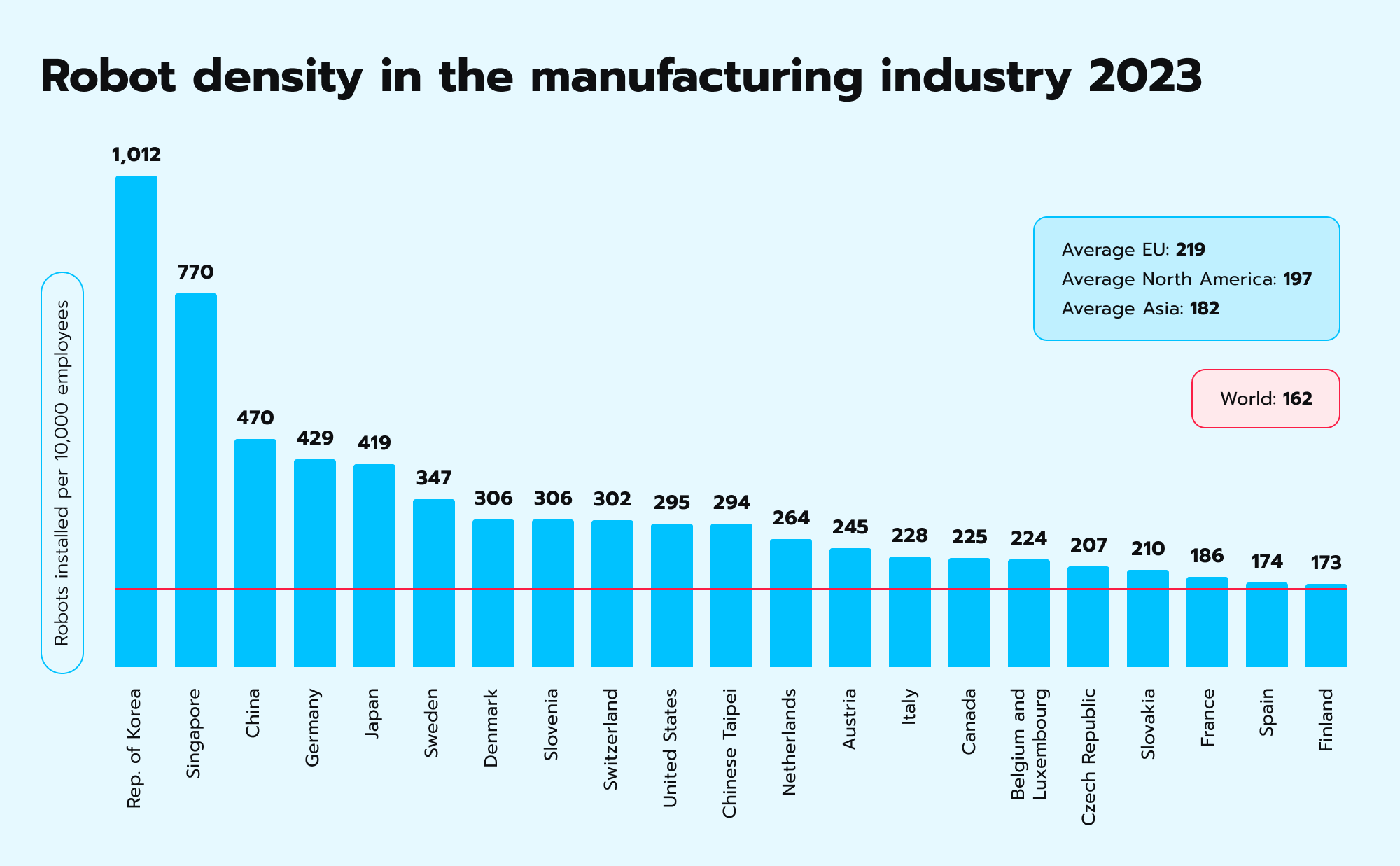
Figure 6. Robot density in the manufacturing industry
Here are some crucial insights to consider when looking closer at the manufacturing trend above:
A boost for the workforce
When robots take on strenuous tasks, human employees can shift to roles that require creativity or oversight. Manufacturers have noted in recent studies that collaboration between humans and machines results in higher quality work. Automated material handling, assembly, and packaging free up workers to focus on more advanced tasks like programming and analytics.
Improved accuracy and speed
Robotics can handle tasks at speeds people cannot match without losing precision. This consistency means fewer defective units and less wasted material. Robotics also helps manufacturers meet tight deadlines, leading to higher customer satisfaction.
Adoption barriers
The initial investment can be expensive, and some small and medium enterprises hesitate due to cost concerns. However, automation often pays off over time through increased throughput and reduced labor costs. As advanced manufacturing continues to grow, experts expect more companies to integrate robotics in some form.
Robotics remains a major driver in the push toward smart manufacturing. By adopting automation, factories reduce manual work, lower the chance of human error, and increase throughput.
8. Advanced data analytics and real-time monitoring
According to recent calculations, about 442 zettabytes of data are generated daily. That’s about 442,817,312,970,506,240,000 bytes or 206,202,880,000 movies (each averaging 2 GB). Considering the rapid amassing of raw data, no industry wants to find a way to analyze data for strategic benefits, and manufacturing is no exception.
Furthermore, manufacturing becomes more data-centric each year. Teams collect enormous volumes of data from sensors, production lines, and supply chain partners. The next step is turning that data into practical insights. Real-time monitoring gives factories the power to optimize every part of the process, from raw materials to finished goods.
Improved decision-making
Data analytics can reveal industrial manufacturing trends that remain hidden without proper review. Production managers can see which equipment slows productivity, which shifts produce the best results, and how to address upcoming bottlenecks. These steps help manufacturers shape the future by acting on facts rather than assumptions.
Inventory management
Large facilities often face challenges with parts storage and inventory turnover. Data analytics platforms analyze daily usage, future orders, and supplier lead times and suggest the ideal inventory levels. This process can minimize waste and reduce holding costs.
Data governance and privacy
As manufacturers rely more on data, data governance policies become crucial. Clear protocols for accessing, using, and protecting data reduce the risk of leaks. This awareness is essential for companies dealing with sensitive or proprietary information, especially when working with multiple partners or suppliers.
9. Predictive maintenance. Cutting unplanned downtime
Predictive maintenance is a game-changer for many organizations (see Fig. 7).
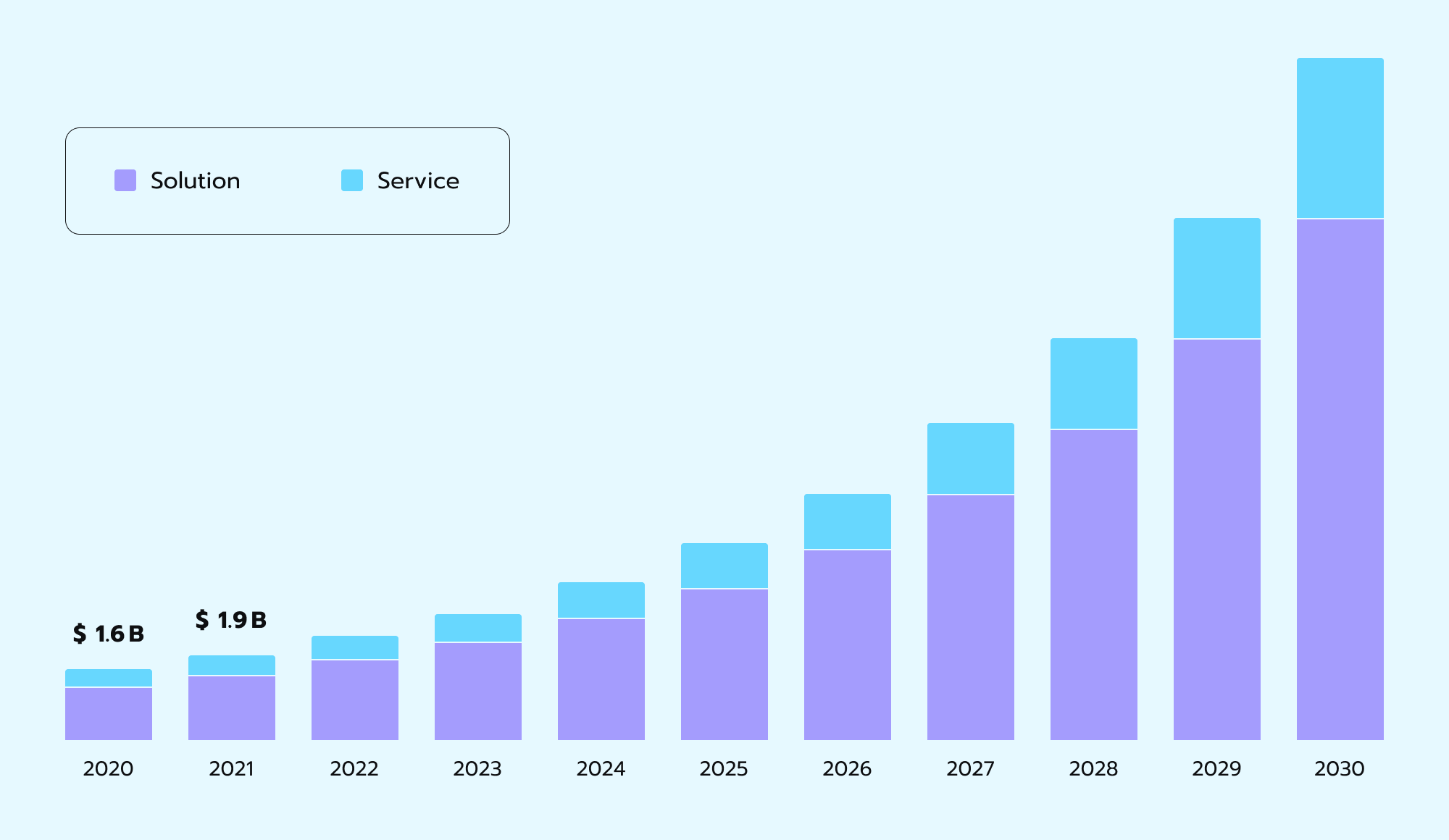
Figure 7. The U.S. predictive maintenance market in USD billion
Factories integrate sensors into their machinery, gather data on temperature, vibration, and other factors, and then use AI-based models to predict failures before they occur. The trend in manufacturing revolutionizes manufacturing by making maintenance more efficient and cost-effective.
Fewer disruptions
Unplanned downtime can halt production and cause delays throughout the supply chain. Predictive maintenance minimizes these surprises by alerting technicians to early warning signs. Repairs can then be scheduled during planned breaks, ensuring the factory remains productive.
Longer machine lifespan
Identifying small issues early can extend the life of manufacturing equipment by years. This approach also reduces the need for last-minute part replacements, which can be pricey. Companies benefit from more stable operations and lower overall maintenance budgets.
Data-driven insights
Predictive maintenance programs rely on data analytics to spot patterns. For instance, a sudden temperature spike might signal that a motor needs lubrication or replacement. By collecting many data points over time, the AI model improves its accuracy. Eventually, it can alert managers to potential concerns well before the machine shows obvious problems.
Predictive maintenance is a top trend on many lists because it helps factories avoid downtime, save money, and maximize the performance of their machines.
10. Cybersecurity in the connected factory
Modern manufacturers depend on digital systems to keep operations flowing. That reliance also makes them targets for cyber threats. Safeguarding networks, machinery, and supply chain data is essential in today’s interconnected environment.
Protecting Operational Technology (OT)
The convergence of IT and OT has brought new cyber risks. Factory equipment was once isolated, but now it often connects to networks for data exchange. Hackers can exploit these connections to disrupt production. Because of this, industrial cybersecurity solutions need to address both the IT side (office software, emails) and the OT side (robots, assembly lines).
Training manufacturing employees
A robust firewall or antivirus system is not always enough. Many breaches occur because of phishing attempts or accidental insider errors. Clear policies and practical training can help employees recognize suspicious activities and take action. Manufacturers and manufacturing institutes often mention cybersecurity as a vital aspect of workforce development.
Standards and compliance
Global manufacturing must comply with various regulations. For example, some automotive manufacturers comply with ISO standards that guide information security practices. Adhering to recognized frameworks fosters trust with partners and customers, especially in high-stakes sectors like aerospace or medical devices.
Cybersecurity is no longer optional. It protects data, safeguards equipment from sabotage, and ensures uninterrupted operations in the connected factory setting.
Practical steps for manufacturers moving forward
Staying ahead in the manufacturing sector doesn’t require an overnight overhaul. Strategic, incremental changes bring results that endure. Below are some practical steps to consider when you consider the takeaways of manufacturing trends:
1. Start small with automation. Factories do not have to automate every station at once. Pilot projects can show clear returns before wider adoption.
2. Use data for decision-making. Data analytics might require new software tools or staff training. Begin with a targeted approach, such as tracking how quickly a key production line meets daily targets.
3. Plan for cybersecurity. An in-house or third-party security audit can uncover weak points. Address them quickly to protect intellectual property and maintain production integrity.
4. Engage the workforce. Employees want to learn new skills. Reskilling programs and clear communication about technology changes boost morale and productivity.
5. Embrace sustainability. Aim for carbon neutrality through energy upgrades, waste reduction, or new material choices. Sustainable approaches can improve brand image and reduce long-term operational costs.
6. Use digital twins and predictive maintenance. These modern tools can decrease downtime and refine operations. Start with a single line or process, and then expand as you see results.
Each factory has unique needs. A phased, thoughtful approach to new technology and methods helps ensure smooth transitions and lasting improvements.
Conclusion
Manufacturing in 2025 will be different from what we see today. Top manufacturing industry trends, including smart factories, AI, green manufacturing, predictive maintenance, digital twin technology, and others, are transforming the industry at every level. Many of these shifts gained momentum during the pandemic, highlighting the need for secure supply chains, flexible operations, and a well-trained workforce.
Companies that invest in sustainability, adopt advanced data analytics, and strengthen cybersecurity will stand out in a competitive market. They will also attract talent that values continuous learning and innovation. While global events may spark more changes, businesses that focus on agility, reduce waste, and capitalize on cutting-edge tools will remain resilient.
Just like any other technology trend, generative AI models have evolved from merely helping people to executing tasks independently and professionally.
Want to learn more about the strategic manufacturing technology trends for 2025 and beyond?
Contact Avenga, your trusted expert in digital transformation and AI development.